Learn How to MIG Weld Stainless Steel at Home or for Industry
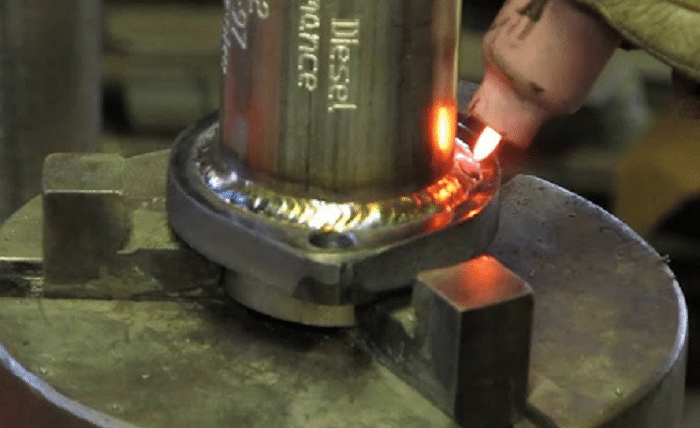
For that reason, MIG welding stainless-steel is an essential know-how for both experts and also Do It Yourself lovers. Ultimately, you can use this technique for a variety of purposes — from converting your home to industrial applications — and knowing how to perform it properly will only improve your weld. Welding stainless steel could be very tricky to do, because it is notorious for being corrosion resistant and requiring certain conditions to make sure it maintains its structure, and design.
Note: Discover the best stainless steel welding wire with us! As an authorized dealer of all major brands used by professionals, we offer the largest stock of welding supplies. Visit our website at https://www.udo.co.th/product/detail/yawata-316l-16 to explore our products or seek expert welding advice from our specialists. Don’t miss out on the highest quality and availability in the market!
From equipment selection to technique application, you will learn the secrets of achieving great results every time when we MIG weld stainless steel in this article. So, whether you want to get better at welding or find quality stainless steel welding materials, this is the guide for you.
Need of MIG Welding Stainless Steel
Metal Inert Gas (MIG) welding is one of the most commonly used methods for its speed and versatility. MIG welding is the method of choice for stainless steel because:
The effectiveness: It offers fast and accurate welds which makes it useful for large-scale tasks.
Wide Thickness Range: MIG welding can also be used on different thicknesses of stainless steel.
Cosmetic Results: The process gives neat and aesthetically appealing welds, which are a vital requirement for projects where appearance matters.
Step 1: Picking The Suitable MIG Welder
Choosing the right equipment is the first step on your journey to perfection results. Here’s what you’ll need:
Good MIG Welder: Get a purpose built machine for stainless steel welding. Voltage and amperage control with adjustable precision are basic features.
Filler Wire: Use filler wire that is of similar grade to your stainless steel. Example: Yawata 316L-16 (shown here). perfect okalu for quality welding.
The ideal shielding gas for stainless steel is a blend of argon and CO2 (with an approximate composition of 98% argon and 2% CO2), which minimizes oxidation, providing you with smooth welds.
Safety gear: Safety comes first and this is not up for debate. Wear a welding helmet, gloves, and protective clothing.
Stainless Steel Preparation — Step Two
If you want to have a successful outcome in MIG welding stainless steel, preparation is your best weapon against failure. Follow these steps:
Surface Preparation: The surface of the stainless steel must be clean and free of contaminants such as dirt, oil, and rust; Clean Using Stainless Steel Brush or Grinder
Clamping: Use clamps to secure the stainless steel parts in position for welding
Edge Preparation: For materials that are thick, you may want to bevel the edges to get better penetration and an overall stronger weld.
Learning the MIG Welding Process: Step 3
When your equipment and materials are in places, then work on perfecting your process. Try These Tips: It Can Make a Difference
Keep the Correct Arc Travel Angle: The torch should be held at a 10–15 angle towards the weld pool. This encourages good penetration and minimizes spatter.
Regulate the Tempo: Have a regular motion of the torch. If you’re too fast, the welds are weak; too slow and you burn through.
Heat Input: Stainless steel is also heat sensitive. How excessive heat can cause warping, discolouration. Raise the voltage and wire feed speed for stable results.
Stitch Welding Approach: Stitch welding means short, spaced welds so be sure to take this into account to limit heat distortion for very thin stainless steel.
Step 4: Post-Welding Care
A few finishing touches after completing the weld ensure longevity:
Examine the welds: Look for cracks, pores or other imperfections. In addition, a perfect weld surface should level.
Clean the Welded Area- Use a stainless steel fiberglass brush or pickling paste to remove discoloration and oxidation.
Polishing: If your project needs a polished look, use a polishing compound to bring back its original shine.
Few Common Challenges and their Solutions
Stainless steel presents unique challenges to MIG welding. Here’s how to address them:
Minimize spatter, by adjusting the wire feed speed and shielding gas flow.
Speaking of looks, stainless steel should look brilliant for its whole life, however due to overheating and not cleaning the weld in time can change this fact.
Cracking: Make sure to use the correct filler wire for your welding process and follow good practice joint preparation procedures to prevent cracking.
The Benefits of Using High-Quality Stainless Steel Welding Supplies
Deciding on materials directly impacts your results in welding. For durability and strength, use Yawata 316L-16 high quality stainless steel filler wires. These supplies are made to support the needs of home tasks, along with industrial jobs, allowing you distinctive dog carriers action on every occasion.
To get the best quality welding supplies, you should check the UDO website. Their extensive selection of industrial welding products means that you will have everything necessary to get the job done.
Conclusion
In many ways the process of MIG welding on stainless steel is nothing more than an art and science. With the right equipment, good preparation and of course your technique it is possible to produce perfect welds every single time. The secret behind people doing home DIY jobs or those doing industrial projects is simply the attention to detail and repetition.
Therefore, in order to learn how to MIG weld stainless steel properly, do yourself a favor and grab some decent tools and materials. Check out UDO’s stainless steel filler wires, and take your welding projects to a new level.