How to Mig Weld Stainless Steel: A Step-by-Step Guide
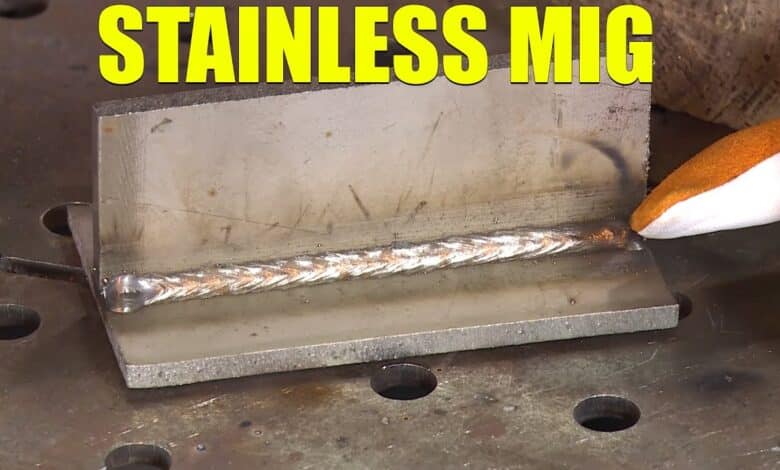
Mig welding stainless steel can seem tricky. But with the right steps, it’s manageable.
This guide will show you how to mig weld stainless steel effectively. Stainless steel is popular in many industries. It offers strength and resistance to rust. But welding it can be challenging. The process requires precision and the right tools.
This introduction will give you a clear understanding of what to expect. You’ll learn about the materials needed and the techniques involved. By the end, you will feel confident to start your welding project. Whether you’re a beginner or have some experience, this guide is for you. Let’s dive into the world of mig welding stainless steel.

Credit: www.millerwelds.com
Introduction To Mig Welding Stainless Steel
MIG welding is a popular method used in various industries. It stands for Metal Inert Gas welding. This technique is effective and widely used for welding stainless steel. It involves using a continuous wire electrode and a shielding gas. The process is simple and offers high-quality welds.
Stainless steel is known for its strength and resistance to corrosion. Using MIG welding on stainless steel ensures durability and precision. This process is suitable for both beginners and experienced welders. It provides a clean and efficient way to join stainless steel parts.
Benefits Of Mig Welding
MIG welding offers many benefits. Here are some key advantages:
- Ease of use: The process is straightforward and easy to learn.
- High efficiency: It provides faster welding speeds and higher productivity.
- Clean welds: Produces less slag, resulting in cleaner welds.
- Versatility: Suitable for both thin and thick materials.
- Cost-effective: Reduces labor costs due to its speed and simplicity.
Applications In Industry
MIG welding stainless steel is used in many industries. Some common applications include:
Industry | Applications |
---|---|
Automotive | Exhaust systems, chassis components |
Construction | Structural frameworks, bridges |
Manufacturing | Machinery, equipment parts |
Food and Beverage | Processing equipment, storage tanks |
Aerospace | Aircraft components, support structures |
These applications highlight the versatility and importance of MIG welding in modern industries. The technique ensures high-quality and reliable welds. It is a valuable skill for many professionals.
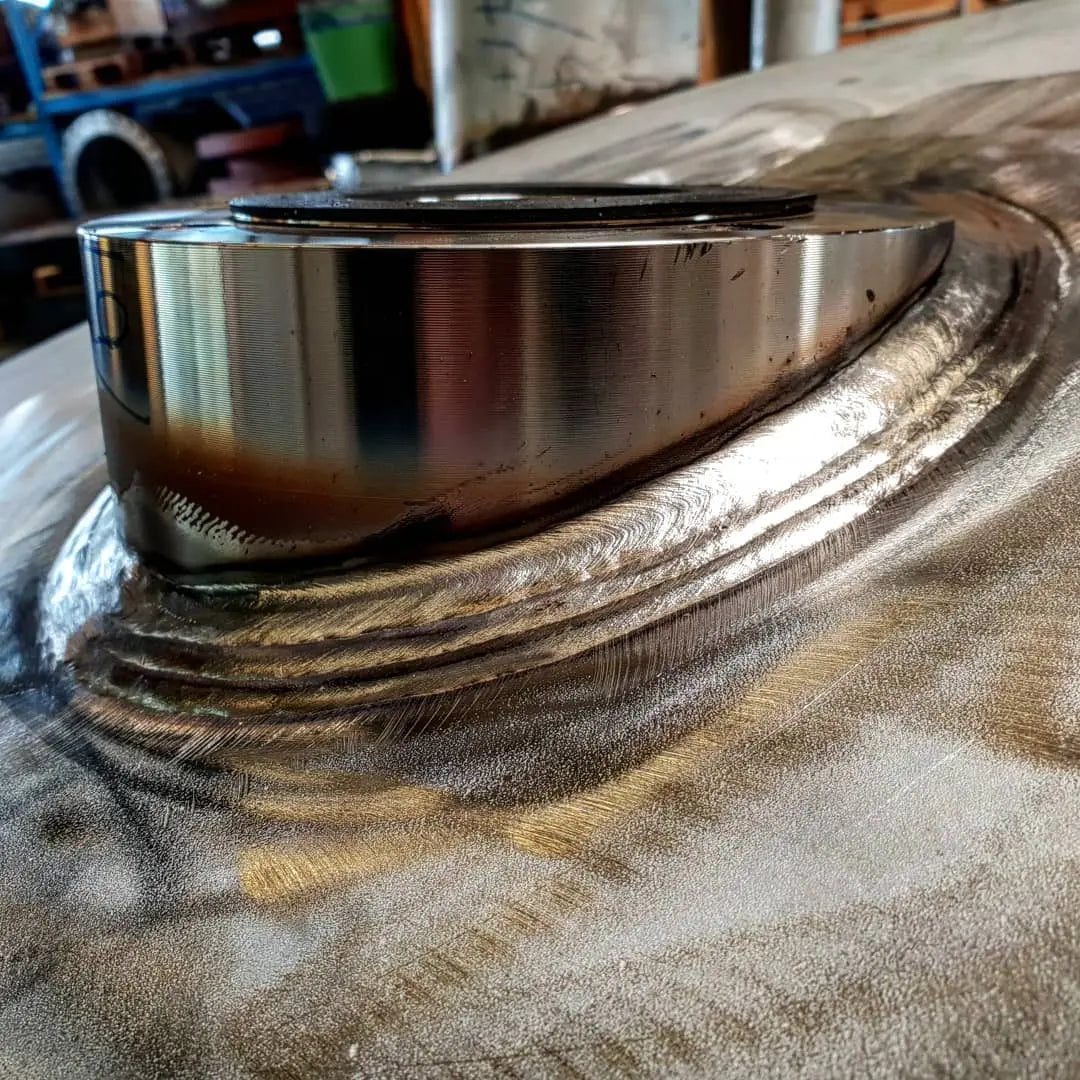
Credit: tooliom.com
Choosing The Right Equipment
Choosing the right equipment is crucial for successful MIG welding of stainless steel. Proper equipment ensures quality welds and reduces complications. Here, we’ll guide you through selecting the right MIG welder, gas, and wire for your project.
Mig Welder Selection
When selecting a MIG welder, consider the thickness of the stainless steel. A welder with adjustable settings is ideal. This allows for precise control over the welding process. Look for a welder with a high duty cycle. This ensures that the welder can handle longer welding sessions without overheating.
Pay attention to the welder’s amperage range. For stainless steel, a range between 150 to 200 amps is often sufficient. Make sure the welder is compatible with the gas and wire you plan to use.
Gas And Wire Requirements
The choice of gas and wire is just as important. Use a gas mix of 90% helium, 7.5% argon, and 2.5% carbon dioxide. This mix provides a stable arc and good penetration. It also reduces oxidation, resulting in cleaner welds.
For the wire, select a stainless steel MIG wire. The most common types are 308L and 316L. These wires are designed specifically for welding stainless steel. They provide strong, corrosion-resistant welds.
Here’s a quick reference table for gas and wire requirements:
Component | Recommendation |
---|---|
Gas Mix | 90% helium, 7.5% argon, 2.5% carbon dioxide |
Wire Type | 308L or 316L stainless steel MIG wire |
Using the correct gas and wire ensures strong, clean welds. It also minimizes spatter and improves overall weld quality.
Preparing Your Workspace
Before you start MIG welding stainless steel, it’s crucial to prepare your workspace. A well-prepared area ensures safety and efficiency. Let’s dive into the essential steps to get your space ready for welding.
Safety Precautions
Safety should always come first. Here are some key safety measures to follow:
- Wear protective gear: Always use a welding helmet, gloves, and a welding jacket.
- Ventilation: Ensure your workspace is well-ventilated to avoid inhaling harmful fumes.
- Fire extinguisher: Keep a fire extinguisher nearby in case of emergencies.
- Remove flammable materials: Clear your workspace of any flammable items to prevent accidents.
Organizing Tools And Materials
Having your tools and materials well-organized makes the welding process smoother. Here are some tips:
- Gather your tools: Ensure you have your MIG welder, wire, and other necessary tools.
- Check your materials: Make sure you have the right type of stainless steel and welding wire.
- Arrange your workspace: Place your tools within easy reach to avoid unnecessary movements.
A tidy workspace helps you stay focused and work efficiently. Use a table to layout your tools and materials if needed.
Tool | Purpose |
---|---|
MIG Welder | Primary tool for welding |
Welding Wire | Filler material for the weld |
Welding Helmet | Protects eyes and face |
Gloves | Protects hands |
Fire Extinguisher | Safety measure for emergencies |
By following these steps, you ensure a safe and efficient welding process. Proper preparation is key to achieving quality results in MIG welding stainless steel.
Setting Up The Mig Welder
Setting up the MIG welder is crucial for successful welding. Proper setup ensures strong and clean welds. This guide will help you set up your MIG welder for welding stainless steel.
Adjusting Voltage And Amperage
First, adjust the voltage. Stainless steel requires a specific voltage range. Check the welder’s manual for the recommended voltage. Set the voltage to match the thickness of the stainless steel. Thicker steel needs higher voltage.
Next, adjust the amperage. Amperage controls the heat of the weld. Use the welder’s chart to find the right amperage. Too high or too low amperage can ruin the weld. Make fine adjustments until you find the sweet spot.
Selecting The Correct Wire Feed Speed
Wire feed speed is another important setting. The speed affects the weld quality. Too fast, and you get a messy weld. Too slow, and the weld will be weak.
Find the recommended wire feed speed in the welder’s manual. Adjust the speed according to the stainless steel thickness. Test the speed on scrap metal first. Make small changes until the weld looks right.
Remember, each welder may vary. Always refer to the specific manual. Practice makes perfect. With the right setup, you’ll achieve strong, clean welds on stainless steel.
Preparing The Stainless Steel
Preparing the stainless steel is a crucial step in MIG welding. Proper preparation ensures strong, clean welds. It involves cleaning the surface and positioning the material correctly.
Cleaning The Surface
First, make sure the stainless steel is clean. Use a wire brush or grinder to remove dirt and debris. Stainless steel must be free of oil, grease, and other contaminants. Use a degreaser if needed. Rinse the surface with water and dry it thoroughly.
Clamping And Positioning
Next, position the stainless steel pieces. Align them as needed for your project. Use clamps to secure the material in place. Proper clamping prevents movement during welding. This helps create accurate and clean welds.
Ensure the pieces are stable. Double-check their alignment before starting. A well-prepared surface and correct positioning make a big difference. It sets the foundation for successful MIG welding.
Executing The Weld
Executing the weld is a crucial part of MIG welding stainless steel. Proper execution ensures a strong and clean weld. This section will guide you through the key steps involved in executing a successful weld.
Starting The Arc
First, position the welding torch at a 90-degree angle to the workpiece. Ensure the wire is close to the starting point. Squeeze the trigger to start the arc. Move the torch smoothly to establish a stable arc. Avoid abrupt movements to prevent arc instability.
Maintaining Proper Technique
Hold the torch at a slight angle, about 10 to 15 degrees. This helps direct the weld pool. Keep a consistent distance between the torch and the workpiece. Too close can cause spatter; too far can weaken the weld. Move the torch steadily along the joint. Aim for a speed that allows the weld pool to form evenly. Watch the weld pool carefully. Adjust your speed and angle as needed. Keep your hand steady to produce a clean, strong weld
Post-welding Procedures
After successfully completing the welding process, it’s crucial to follow the right post-welding procedures. These steps ensure the durability and appearance of your stainless steel welds. Let’s explore the key post-welding procedures to achieve the best results.
Inspecting The Weld
First, inspect the weld visually. Look for any cracks, gaps, or inconsistencies. Ensure the weld bead is even and smooth. Check for any signs of contamination or discoloration.
Use a magnifying glass if needed. Pay attention to the edges and joints. A thorough inspection helps identify issues early. This can prevent future failures.
Cleaning And Polishing
Next, clean the weld area. Remove any slag or spatter using a wire brush. Stainless steel brushes work best. Avoid using carbon steel brushes, as they can contaminate the stainless steel.
After cleaning, polish the weld. Use a stainless steel polishing compound. This improves the appearance and corrosion resistance. Apply the compound with a soft cloth or polishing wheel.
Finally, wipe down the area with a clean, dry cloth. This removes any remaining residue and gives the weld a professional finish.
Common Issues And Troubleshooting
MIG welding stainless steel can be tricky. Several common issues can arise during the process. Understanding these problems and knowing how to fix them is crucial. Here, we will discuss some frequent issues and their solutions.
Dealing With Warping
Warping occurs when the metal bends due to heat. This is a common problem in MIG welding stainless steel. To prevent warping, you can:
- Use clamps to hold the metal in place.
- Employ a backing bar to absorb heat.
- Weld in short sections to control heat spread.
- Use a low heat setting on your welder.
If warping still occurs, you can try to straighten the metal using a hammer and anvil. This can help to reshape the metal without causing further damage.
Fixing Porosity And Cracks
Porosity and cracks are often caused by contaminants or improper welding techniques. To fix these issues, follow these steps:
- Ensure the metal is clean and free of oil, grease, and dirt. Use a wire brush or grinder.
- Check your gas flow. Make sure the shielding gas is flowing correctly. Use a flow meter to adjust the settings.
- Maintain a proper torch angle. Hold the torch at a 10-15 degree angle to the workpiece.
- Use the correct filler material. Ensure it matches the type of stainless steel you are welding.
If cracks appear, grind out the affected area and re-weld. This helps to ensure a strong bond and prevents further cracking.
Tips For Improving Weld Quality
Improving the quality of your MIG welds on stainless steel is crucial for strong, clean, and durable results. Here are some essential tips to help you achieve high-quality welds every time.
Consistent Practice
Practice regularly to develop a steady hand and consistent technique. Set up a welding schedule and stick to it. Focus on the following:
- Maintaining a steady travel speed
- Keeping the welding gun at a consistent angle
- Ensuring a uniform bead width
Practicing on scrap pieces of stainless steel can help you hone your skills. Track your progress and make adjustments as needed.
Proper Maintenance Of Equipment
Regular maintenance of your welding equipment is essential for optimal performance. Ensure your equipment is clean and in good working condition. Pay attention to:
- Welding gun: Clean the nozzle and check for wear and tear.
- Wire feed: Ensure the wire feed is smooth and consistent.
- Gas flow: Verify that the gas flow rate is correct.
Replace worn-out parts to avoid poor welds and equipment malfunctions. Keep a maintenance log to track the condition of your equipment.
Equipment | Maintenance Frequency |
---|---|
Welding Gun | Weekly |
Wire Feed | Monthly |
Gas Flow | Before Each Use |

Credit: www.youtube.com
Frequently Asked Questions
What Is Mig Welding?
MIG welding, or Metal Inert Gas welding, is a process using a continuous wire feed and a shielding gas. This method is popular for its efficiency and ease of use.
Can You Mig Weld Stainless Steel?
Yes, MIG welding stainless steel is possible. It requires a specific type of wire and shielding gas. Proper technique ensures strong, corrosion-resistant welds.
What Gas Is Used For Mig Welding Stainless Steel?
Argon mixed with carbon dioxide or helium is commonly used. This mixture provides the necessary shield to protect the weld from contamination.
What Wire Is Best For Mig Welding Stainless Steel?
Use stainless steel wire, typically 308, 309, or 316 grade. The choice depends on the base material and application.
Conclusion
MIG welding stainless steel can be straightforward with the right approach. Always remember to clean the metal well. Use the correct gas mixture for best results. Practice helps to improve your technique. Safety should always be your top priority. Proper preparation and patience lead to better welds.
Keep learning and refining your skills. Happy welding!